Operations manager Leslee Barker is the first to tell you she and her team are excited to continue learning about the new Colter & Peterson SABER paper cutters that now occupy space at Miller Zell in Atlanta. But they couldn’t be happier with the early results of the automated 62-inch SABER® X-15 and 126-inch SABER XXL machines that came equipped with advanced Microcut® software.
The X-15 was the first to be installed in March, followed by the XXL in early May. Barker said they replaced two older machines, a 144-inch Cauhe guillotine purchased new in 1998, and a reconditioned 110-inch Lawson guillotine cutter that was bought in 2009. Both older machines were installed by Colter & Peterson, a Miller Zell vendor for 21 years.
She said the new paper cutters arrived at an opportune time; Miller Zell’s busiest production time of the year runs from March through October. That means the 315,000 square foot operation runs two shifts, up to seven days a week.
“With the older machines, we used the larger cutter to cut twelve-foot boards, which is work our customers don’t currently do,” said Barker. “Those machines could not handle tight tolerances or thin substrates the way we need them to. One of our supervisors did some research before he reached out to Richard Peereboom at Colter & Peterson, and one of our service technicians also recommended them because of their expertise with cutters.”
Industry Leaders Combine to Produce Work on a Higher Level
Miller Zell provides strategy, store design, signage, merchandising, fixtures, POP, digital, and execution capabilities, in addition to large format expertise in retail printing, for customers throughout North America and in Puerto Rico. So highly respected, they handle the majority of printing for a large southern based big-box chain.
In the retail world, things can change overnight. Miller Zell not only has the capability to manage it, they often exceed the highest expectations of their customers.
“Today, we’re printing a variety of quantities, substrates and sizes. We are using the paper cutters for shelf strip work, among other jobs. The shelf strip type of work is where the flexibility of the SABER paper cutters is paying off,” remarked Calvin Hale, Miller Zell’s production supervisor. “Overall, their performance has been amazing so far. We’ve used them to cut a variety of substrates, from vinyl, styrene, and ultraboard to boards stock and PETG. The 126-inch cutter will handle the majority of the work but the smaller one will trim material down to smaller sizes. Compared to the machines they replaced, we’re getting much more consistent cutting.”
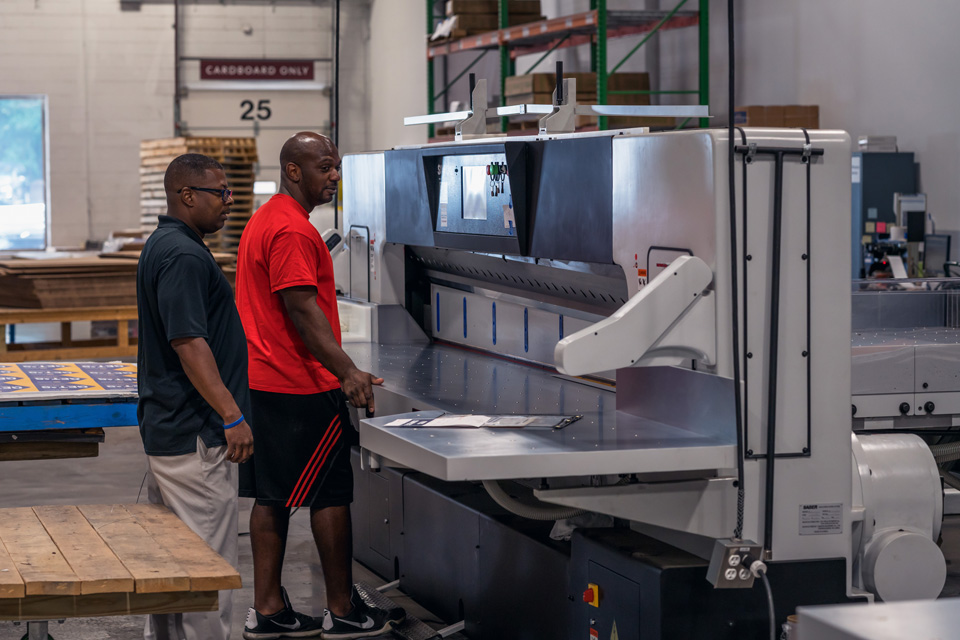
Cutter operator Brandon Coleman could not contain his excitement about the new machines.
“The accuracy is 100 percent. It hits the nail every time,” he said. “The SABERs have a laser beam that lets you know when to make your cut. The tables the paper stacks rest on push out more air than the older paper cutters, which makes it easier to move or jog the load. The backguage on the old 144-inch cutter had a tunnel in the middle of the table. If the material was thin enough, it could get kinked or damaged. Now it’s a lot easier to move the stacks around to the point where we are kind of spoiled.”
“The shelf strips,” added Hale, “are 1-1/8 and 1-3/16 inches thick and there are no issues with consistency between cuts. Since the stack lifts are tall and can accommodate five inches of material, we are cutting 25 to 30 sheets at a time, depending on the stock thickness. The SABERs are faster, smarter, and we love them. We print filler panel blanks and do them by the thousands. A job like that is now completed in half the time.”
The increased level of productivity is due to Microcut, a standard feature on all new Colter & Peterson SABER and PRISM paper cutters. Most shops, once they gain experience and understand all Microcut has to offer, often report a 50 percent rise in productivity. More work in less time makes an impression on a company’s bottom line.
“The automated programs save us time during set up and move jobs from other cutting processes, which allows us to produce more work in the same amount of time,” said Barker. The SABERs are cutting work produced on state-of-the-art large format printing presses that include a Thieme 6-color inline screen press, a Durst Rho 1312, an Inca X2 & S50, and three EFI HS125 digital presses.
“The good thing,” continued Baker, “is we’re still learning about the capabilities of those cutters and what all they will allow us to move from our other cutting processes.”
One key thing Hale has learned, in addition to the versatility each SABER has to offer, is how simple it is to do maintenance on the machines.
“It’s an easy machine to maintain. It has programs to keep track of all your cuts and save that information for future jobs. It also has codes that let you know when to do required maintenance. We haven’t had to change any blade changes yet. The blade itself has a much sharper edge than the machines it replaced. I understand it is quicker to change out these blades.
“As Leslee said, we will continue to evolve and learn better ways to gain efficiencies to deliver the best products for our customers,” summed up Hale. “We will continue to use the cutters and figure out better ways to increase our throughput with the SABERs every day. It’s great to have the kind of control and flexibility we have with these machines.”
—Press Release