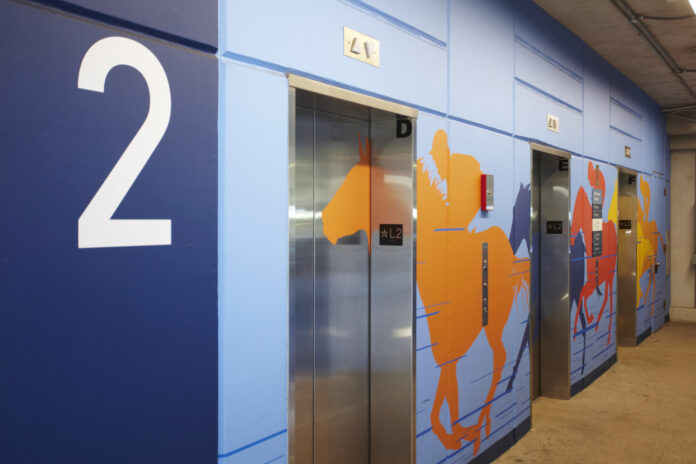
This feature was originally published in Sign Builder Illustrated‘s June 2024 edition.
Two years and counting. Nine hundred permanent, individual signs. More than 12,700 square feet of digitally printed vinyl. Nearly four tons of 1/8-inch aluminum. If you laid out all the signs that Signarama Louisville Downtown in Kentucky has created for a local airport end-to-end, it would be over a mile long.
It all started by submitting a bid for one part of the project to a construction company, which had bid for parking garage work at Louisville Muhammad Ali International Airport back in 2022. By building a relationship with them, as well as the design firm and airport, Signarama Louisville Downtown President and CEO Maggie Harlow has been able to bid on other parts too. And those parts have added up.
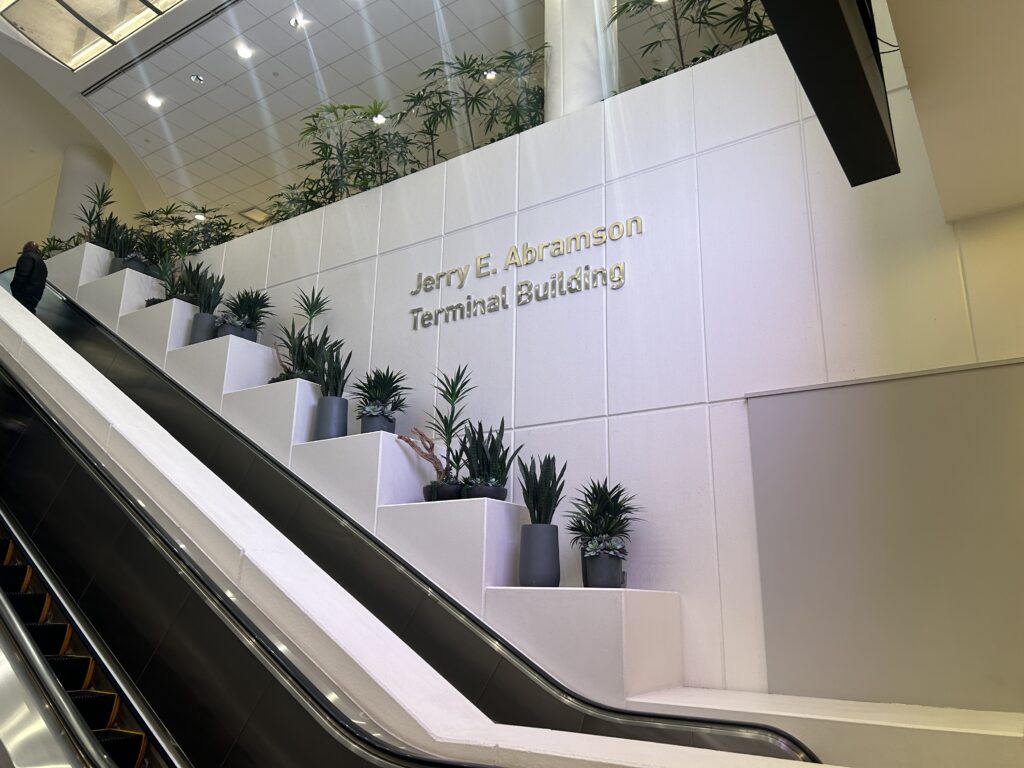
When developing the signs, Harlow’s team followed the vision of Canadian experiential design firm Entro, which had created the airport’s overall visual strategy, providing feedback and advice related to final material choices and some design details.
Entro designed the murals at the elevator vestibules, a graphic likely inspired by the city’s Kentucky Derby. “We worked closely with them to figure out how to prep the wall with paint, reconfigure the design for two layers including [the] background and the horses,” Harlow explains. Her team used high-tack vinyl and a lot of heat and pressure to create the effect.
The wall had to be prepped by knocking down imperfections in the concrete surface. “Luckily the garage has two elevator banks, so the airport worked with us by shutting them down one at a time to allow us to work uninterrupted as much as possible,” Harlow recalls. “We have concerns about [the] long-term durability of the graphics, as folks toting suitcases, etc., are likely to mark up the surfaces. We debated with the client whether this should be painted instead of printed.” In the end, the decision was made to proceed with vinyl— Arlon 8200—printed on an HP 360 with horse outlines trimmed out by a Graphtec cutter.
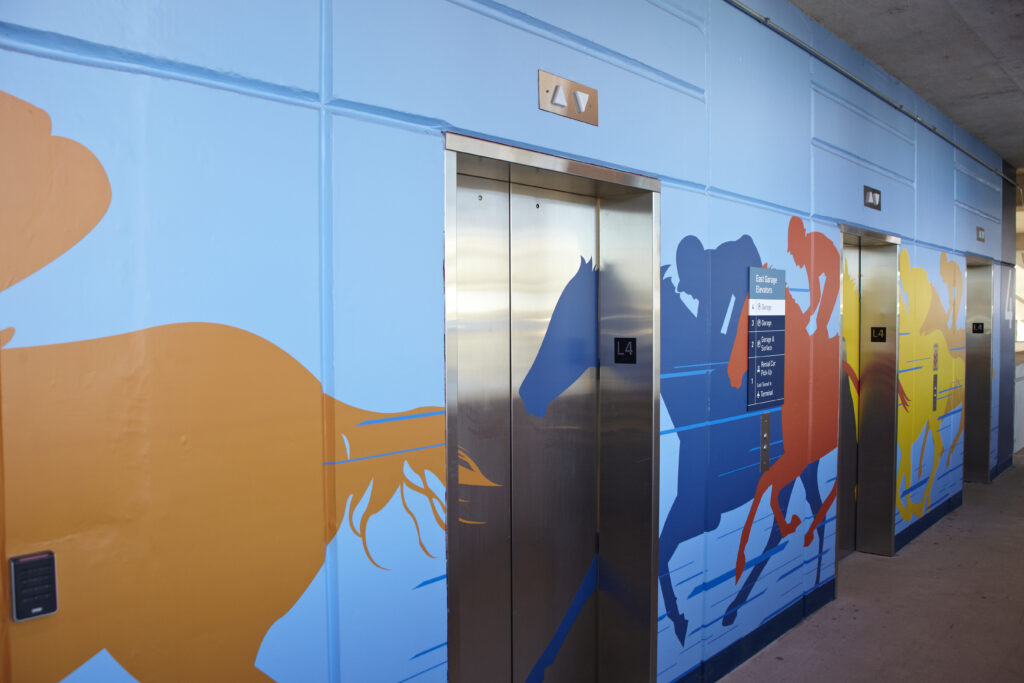
Meanwhile, travelers going up or down the escalators in the Jerry E. Abramson Terminal Building are greeted by a different sign: dimensional letters signaling the locale. Fabricated by Gemini from cast aluminum with a clear finish, the letters are stud mounted into the wall. “…it was a tricky installation that required ladder access and patience to work during normal operating hours,” Harlow explains.
Installing simple parking garage graphics proved to be one of the most challenging parts of the project, requiring significant prep time. “These concrete walls were covered in a decade’s worth of dirt and debris,” Signarama Downtown Louisville Project Manager Keith Watkins says. “We employed bristle brushes to knock this down, a leaf blower to clean it off and alcohol/towels to prep the surface. This also was the case for all of the concrete columns.”
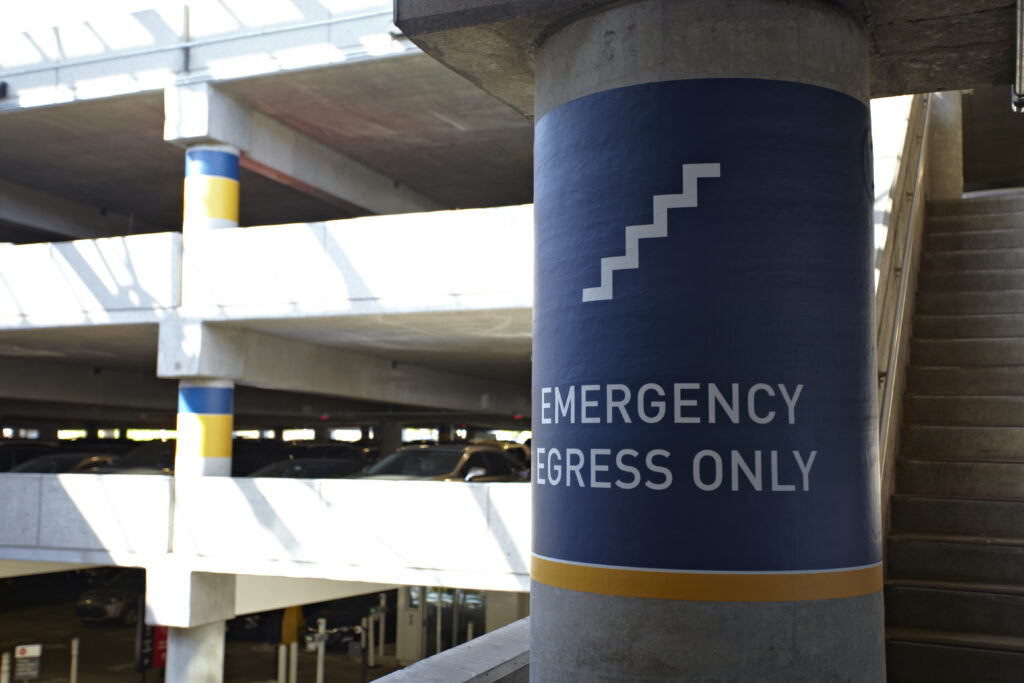
The team used Arlon 1105 conformable material for the column wraps, again printed on HP 360 and cut with a Graphtec machine. “All [print graphics were] matte laminate to help hide surface imperfections,” Harlow notes.
But the most difficult aspects of the parking garage graphics were timing and temperatures. “We had to recruit additional part-time installers to get the work done before the cold temperatures arrived in the fall,” Harlow recalls. Her team had to teach inexperienced installers how to wrap concrete in the low temperatures of the garage, which was significantly colder than outside.
“Sometimes we had four to six people on-site at one time,” Harlow adds. “Because a parking garage is repetitive in appearance, making sure the correct sign is installed in the correct place is an exercise in focus and management. In addition, the work was being inspected by management and by the design firm, so we wanted to be sure every installation was as perfect as possible.”
When it comes to installation, “Necessity is the mother of invention,” Training Manager Thomas Nance says. “The bulkheads throughout the parking garage were just the right height to use a pickup truck as the primary install platform,” he explains. “Standing in the bed of the truck allowed two installers to easily mount the long bulkhead signage throughout the garage. We fabricated a simple tray/shelf that was supported by the ladder rack and provided a place for hammer drills, drivers and fasteners to be placed. A rigid template also evolved that simplified the placement, leveling and drilling for fasteners.”
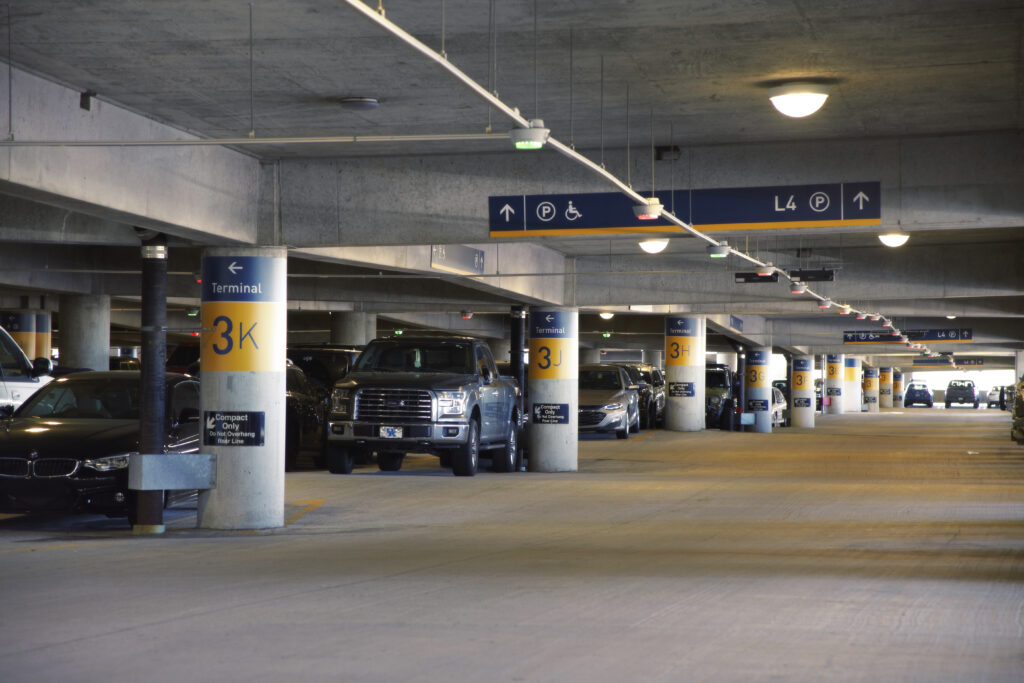
In the parking lot, blue signs proved to be an engineering challenge, as the airport had existing concrete pylons to mount to. “We elected to design a custom post that would mount securely to the attachment point and allow a double-sided mount for the panels that would endure extreme winds and exposure,” Harlow explains. “The elevation of the appearance is because of the quality of the design work,” she adds. “Sometimes good design will elevate the most ordinary of materials.”
For the exit ramps, fabrication was relatively standard: .080 aluminum with a digital print wrap. Signarama Louisville Downtown fabricated the Uber and Lyft signs in house with aluminum composite (ACP) panel, creating a box, then wrapped them with Arlon 1105 with a matte laminate.
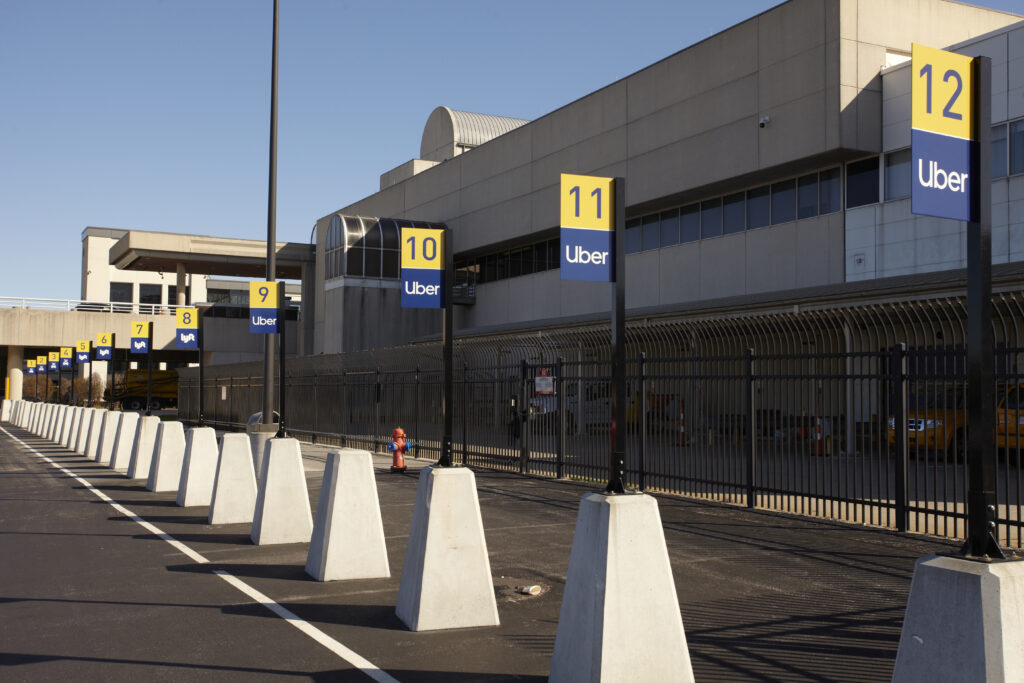
The sign shop tapped local company Integrity Signs to fabricate the exterior monument signs. “A lot of effort was made by the team to ensure the final look was correct,” Harlow says. “The design firm planned … for prototypes to be made of virtually every product, and then did an on-site inspection to be sure their vision was executed and any last details could be sorted out before final production,” she adds. “The [fully painted aluminum] monument signs were designed to be sleek, but also to allow both faces to be removed for servicing or updates.”
For her squad, working in an environment that never closes was a major feat. Airport visitors who spotted team members in their yellow visibility vests assumed they could give directions. “Everyone working on the site became expert in directing people, and dodging traffic,” Harlow says. The installation in the rental car area had to happen at 3 a.m. to reduce traffic interruptions.
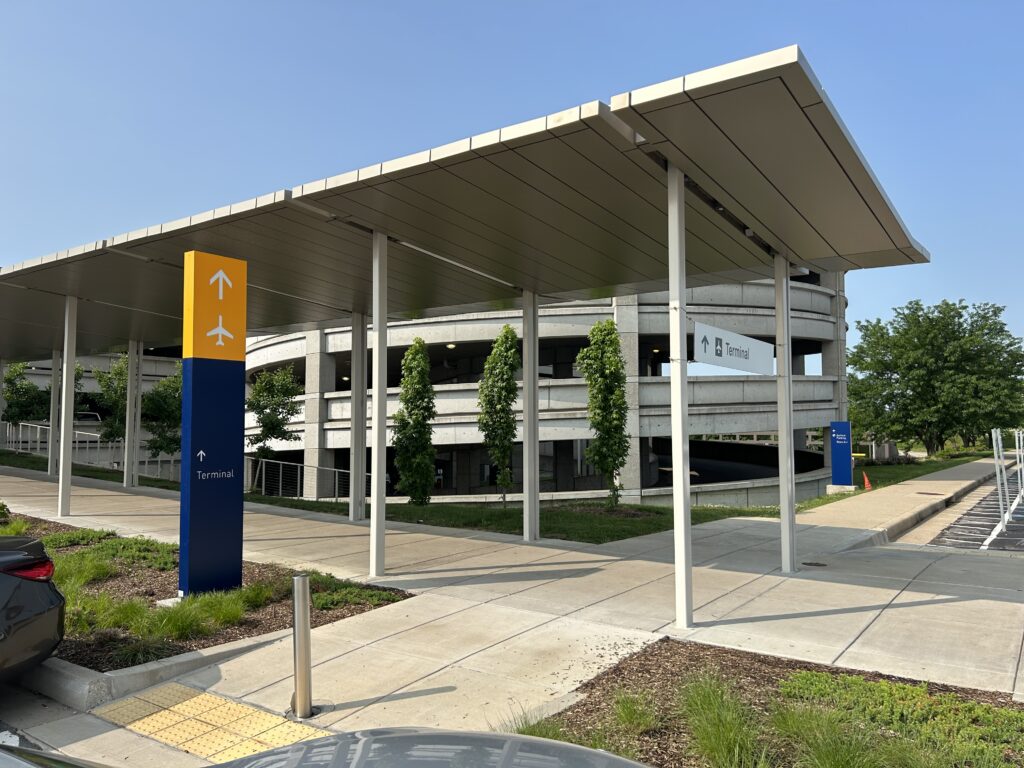
When one undertakes a project of this scope—with tight timeframes, massive volume and multiple organizations involved—Harlow’s team has two recommendations:
First, be flexible in the moment. “Things will change and go wrong. You might end up having to innovate and produce an answer you never would have before,” Harlow says. “Hiring temp workers to install column wraps wouldn’t occur to us until circumstances forced us to innovate. And it worked surprisingly well.”
And second, ask lots of questions. “Don’t assume anything,” Harlow urges. She says it’s especially important to know who is in control of the areas where you’re working. “Know who are decision makers and try to connect with them in advance,” she advises.