As the signage industry begins to adopt Industry 4.0 technologies (AI, loT, and digital tools), it’s essential to understand some manufacturing jargon that may be unfamiliar. While these concepts may seem daunting, they are crucial for the long-term success of your business.
So let’s dive in and learn about Overall Equipment Effectiveness!
Overall Equipment Effectiveness (OEE) is a metric used to measure the effectiveness of manufacturing processes or individual equipment. It considers three factors: Availability (actual production time vs. planned); Performance (equipment performance vs. maximum potential); and Quality (production rate of “good count” products).
The OEE is calculated by multiplying scores of these three factors, resulting in a percentage value that indicates the equipment’s or process’s overall effectiveness.
It is widely used in manufacturing industries to identify areas for optimization, track improvements, and benchmark different equipment and production lines. With Industry 4.0, IoT devices provide real-time data to gauge and improve OEE.
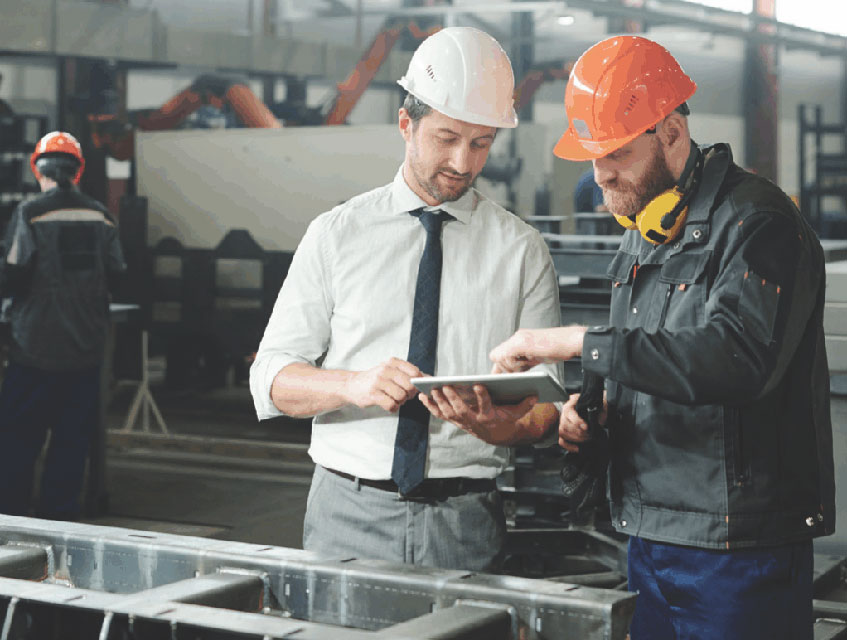
Benefits of Improving OEE
Improving Overall Equipment Effectiveness has many benefits for sign manufacturing organizations, such as:
- Improved productivity
- Improved efficiency
- Cost reduction
- Enhanced quality
- Better decision-making
- Increased capacity
- Equipment reliability and longevity
By optimizing equipment utilization, reducing downtime, and minimizing quality issues, sign shops can achieve higher production rates and output, improve overall efficiency, reduce costs, and produce exceptional products that meet or exceed customer expectations.
Monitoring and analyzing OEE metrics provide valuable insights into equipment performance and production processes, enabling data-driven decision-making and increasing the overall capacity of the production system.
Finally improving OEE often involves proactive maintenance and care for equipment, which can improve equipment reliability, extend equipment lifespan, and reduce the risk of unexpected breakdowns.
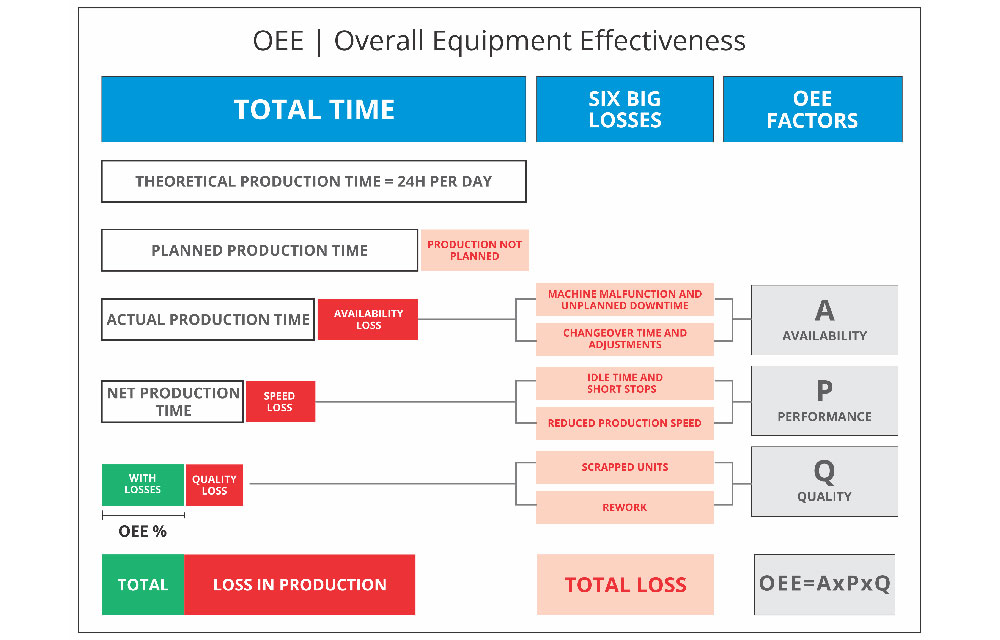
How to Improve OEE
Improving Overall Equipment Effectiveness requires a systematic approach. The following items are key strategies and practices to help you maintain world-class OEE:
Measure and track OEE: Start by measuring and tracking OEE accurately for your equipment and production processes. Establish a current condition baseline and set goals for improvement. Use OEE as a performance metric to monitor progress and identify areas that need attention.
Focus on availability: Address equipment downtime and maximize equipment availability. Implement preventive maintenance programs to minimize breakdowns and schedule maintenance activities during planned stops.
Be sure to optimize changeover processes to reduce setup time and improve equipment utilization.
Enhanced performance: Look for opportunities to optimize equipment performance. Identify and address factors such as availability losses, speed losses, and idle time that impact overall performance.
Implement training programs to ensure that your operators have the necessary skills to operate equipment efficiently.
Improve quality: Quality losses can significantly impact OEE. Focus on reducing defects, rework, and scrap.
Implement quality control measures, conduct root cause analysis for defects, adopt computer vision technologies to detect anomalies, and ensure quality in manufacturing and production processes.
Administer corrective actions to improve product quality and reduce waste.
Implement autonomous maintenance: Empower operators to take ownership of the equipment through autonomous maintenance practices. Remotely monitor assets from IoT sensors and devices and deploy computer vision at the edge, reducing reliance on maintenance teams and minimizing downtime.
Put into action OEE-driven maintenance: Use OEE data to prioritize maintenance activities. Focus on critical equipment or components that have a significant impact on OEE.
Enact predictive maintenance strategies by leveraging condition monitoring techniques and real-time data to detect potential equipment failures.
Continuous improvement culture: Foster a culture of continuous improvement throughout the organization.
Implement structured improvement initiatives such as Kaizen events, Six Sigma projects, or lean manufacturing methodologies to drive ongoing improvement efforts.
Data-driven decision making: Utilize data analytics to gain insights into the factors affecting OEE.
Analyze OEE trends, identify patterns, and use data to make informed decisions about equipment upgrades, process optimizations, or resource allocation.
Leverage advanced analytics and predictive models to identify potential areas for improvement.
Employee engagement and training: Engage and train employees at all levels to drive OEE improvements. Ensure they understand the importance of OEE, provide them with the necessary training and resources to perform their roles effectively, and involve them in meaningful initiatives. Encourage collaboration and knowledge sharing among teams.
Continuous monitoring and review: OEE improvement is an ongoing process. Continuously monitor OEE, track performance, and review progress against targets. Regularly assess the effectiveness of implemented improvements and adjust as needed. Stay proactive in identifying new improvement opportunities.
Remember that OEE score improvement is a long-term endeavor that requires commitment, collaboration, and relentless focus on continuous improvement.
It is essential to involve all stakeholders (from operators to managers) and celebrate company wins to maintain motivation and engagement.
Challenges for Improving OEE
Improving Overall Equipment Effectiveness can bring numerous benefits, but organizations may encounter several common challenges when implementing and optimizing this metric.
Overall Equipment Effectiveness improvements need a culture of continuous improvement, employee engagement, and effective communication. Resistance to change, lack of buy-in, and a focus on short-term productivity over long-term efficiency can hinder OEE initiatives.
Meanwhile managing OEE for modern production equipment can prove challenging due to its complexity and variability. Developing standardized OEE metrics to account for different equipment configurations can be complex.
Another challenge for organizations can be understanding OEE metrics. Proper training and education can help you identify underlying causes of low OEE and prioritize improvement efforts.
Finding the root causes of low OEE is also challenging. It needs a systematic approach, data analysis, and stakeholder collaboration (including operators, maintenance personnel, and process engineers). Identifying the underlying issues accurately is crucial for implementing practical corrective actions.
There can be a struggle to assess and integrate real-time production data from different systems and sources, including legacy equipment that may require additional connectivity and sensors.
Maintaining initial improvements in OEE is another potential roadblock. Ongoing measurement and analysis are necessary to maintain these improvements.
Reliable data collection is essential for accurate OEE calculation. However manual data entry and inadequate tracking systems can lead to inaccuracies and incomplete information, affecting the reliability of OEE measurements.
Balancing OEE (Availability, Performance, and Quality) is crucial, as improving one aspect may lead to other exchanges and affect the overall impact on customer satisfaction.
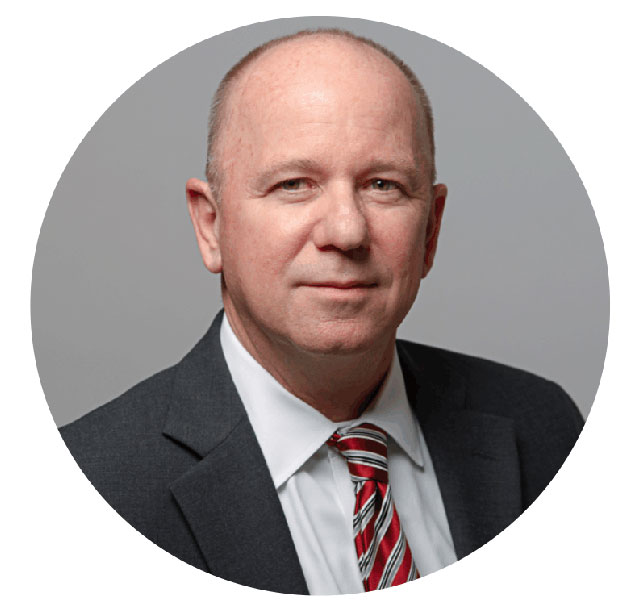
Conclusion
Organizations can effectively implement OEE by proactively identifying and resolving challenges. This approach leads to consistent improvements in equipment efficiency and overall productivity.
Understanding various terms related to OEE are commonly used in discussions and analyses of equipment and manufacturing performance and aid organizations in identifying and addressing areas of improvement to enhance equipment efficiency, throughput, and overall manufacturing performance.
Though it may seem overwhelming, understanding OEE principles and adopting the related language can help teams make significant progress toward making operational efficiency a competitive advantage.
John Hackley has more than thirty-five years of experience in build-to-order sign manufacturing. He currently owns and works as a consultant for Oculus Business Solutions. John also advises on lean production and Industry 4.0 strategies that can help your business grow and become more profitable.