Manufacturing braille/ADA (Americans with Disabilities Act) compliant signage requires precision, uniformity, color-matching technique, efficiency and more. When your shop wins an ADA signage project bid, it’s a great win for your business. But after the shine of the sale wears off, one quickly realizes that there’s a lot of precise work to be done.
Because interpreting braille/ADA signs is so critical to the public, manufacturing them can be a serious deal. Sign shops across America are much more responsible for creating paths of accessibility than the average person thinks. Every time you’re searching for a restroom in a public setting, looking for your doctor’s office or navigating around a school campus, braille/ADA signage helps you reach your destination. And of course, visual disabilities sign indicators play a critical role in equal accessibility across the nation.
Manufacturing signs for the visually impaired that meet the ADA are extremely important and a federal civil rights law. Ink tipping or foil stamping over a required raised surface to achieve colors can be quite difficult to do uniformly, and it involves a lot of precision, taping and cleanup. Sometimes shops have had to scrap finished sign packages during production due to misprints or bad coverage over large surface areas. Your employees may do their best to achieve perfection in this area, but it can be difficult at times and induces stress.
Brad Sorrow, National Sales Executive at Nova Polymers, noticed this and began to develop the concept of a new way to finish the braille cells on ADA signage.
“In the past we’ve always sold a hot stamp unit that uses foils for tipping. You’re very limited on colors and it’s really hard to make the foil apply evenly over large areas, like bathroom gender signs or large pictograms in general” says Sorrow. “More recently, I was able to locate a manufacturer that was willing to engineer my idea into a working machine.”
The “machine” Sorrow refers to is Nova Polymer’s Color Pro, an automated color ink tipping applicating machine for braille/ADA signage that replaces the need for either hot stamping or silk screening.
“This takes the place of hot stamping and silk screening. So, if you’re doing traditional silk screening where you’ve got a screen and you’re pouring ink on it and you’re running a squeegee across, this takes the place of that,” says Sorrow.
“Sign fabricators are used to either ink screening or they might be doing tipping through applying hot stamp foils,” says Nova Polymers Director of Sales and Marketing Tim Lloyd.
“So, what the Color Pro provides is the ability to ink tip all raised areas of a braille cell in just two to three seconds. It consistently rolls ink over all the raised characters as well as the larger pictograms. If you need to run it through a second time just to get color opacity, it’s only two or three more seconds again,” Lloyd adds. “You’re really looking at production cost savings and labor savings. In short, the Color Pro reduces the production time to tip all your ADA signage.”
Becoming proficient in braille/ADA-compliant signage manufacturing can lead to significant new business if you’re able to grasp it and lock in a standard operating process. Adding a machine like the Color Pro to your operation can free up your team to work on other important jobs while the machine relieves you of ink tipping precision worries.
“Schools, hotels, all of your office buildings, hospitals, anywhere that the public goes, are required to have ADA signage,” says Sorrow.
With the capability of consistently producing 100% compliant braille/ADA signage in your shop, you can now go after clients required to have signage that upholds to the Americans with Disabilities Act. And in terms of day-to-day production operations, the Color Pro is easy to train new and inexperienced screeners on.
“Since COVID, one of the biggest challenges within the sign industry is finding a skilled labor force. Sign fabricators have expressed frustrations with the inability not only to find experienced screeners, but with the time it takes to train them and keep them before they leave,” says Lloyd. “It’s really a serious problem. I know that sounds kind of cliché, but the Color Pro provides an exclusive solution to that problem.”
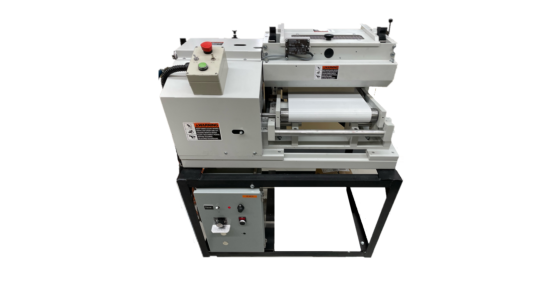
So, what does equipping your shop with this new technology look like?
“When you think of a job with 100 signs, and it’s taking only two to three seconds per sign for ink tipping, think how fast you could do that full production run of signs,” says Lloyd.